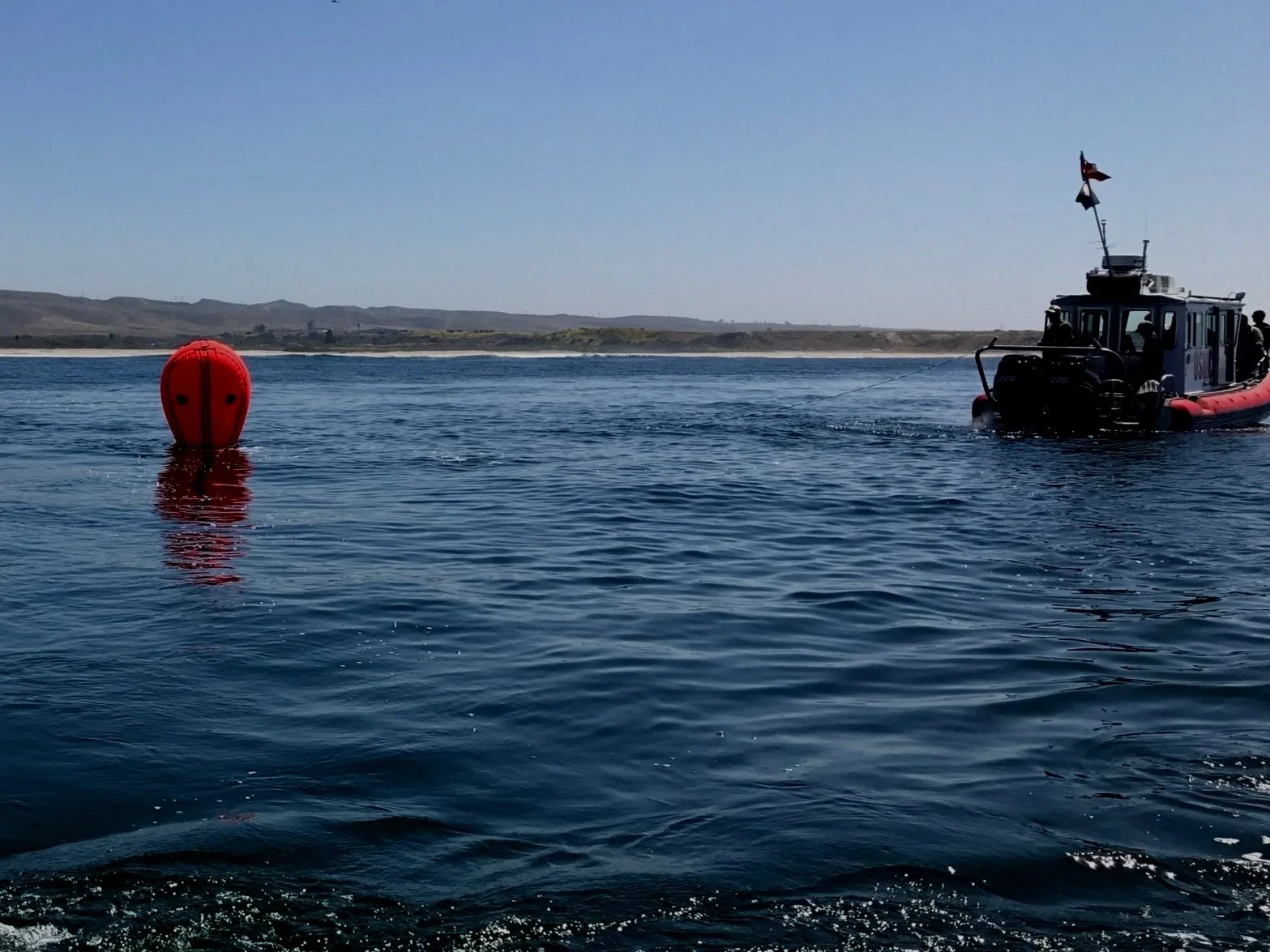
STT specializes in undersea inflated lift systems to be deployed by either an operator or remotely operated vehicle (ROV). Developed for use in a wide range of battlespaces, including non-permissive or combat, expeditionary, and administrative environments.
Designed through the lens of the operator, our systems were developed specifically with the needs of conducting offset lifts in rugged surf and undersea terrain, with durability and reset features to do it over and over again.
Explore the site and see how we have used technology, experience and creativity to build a suite of systems engineered specifically for the rigors and challenges associated with these missions, and the logistical challenges of supporting them.
Mission Driven Technology
Originally developed in cooperation with US Navy Explosive Ordnance Disposal leadership, the STT MCM systems range from deepest depth, highest capacity to expeditionary systems designed to be parachuted if necessary.
MCM Family of Systems
CRNE.2 - Combat, Recovery, Neutralization, Exploitation System MK II
2200 # (WET) lift capacity from 300’ of seawater. ATAC compatible, contains 4x100 cubic foot scuba bottles and the proprietary STT Inflation Valve Assembly
ExLB.2 - Expeditionary Lift Balloon MK II
750 # (WET) lift capacity from 220’ of seawater. ATAC compatible, contains 2x50 cubic foot scuba bottles and the proprietary STT Inflation Valve Assembly
DLBA - Dual Lift Bridge Assembly
The Dual Lift Bridge Assembly was designed to increase the mission capability of the ExLB system, allowing a pair of them to double their lift capacity with the same deployment complexity as a single system. Uses the dual initiation capability of the ATAC to fire both systems with only one shuttle on the shape. Weighs under 30#, is made of rugged aluminum and works with CRNE and CRNE.2 systems.
1500 # (WET) lift capacity from 220’ of seawater. ATAC compatible, uses two ExLB.2 systems, containing 2x50 cubic foot scuba bottles each.
ATAC - Automated Tow Actuated Coupler
The ATAC system attaches to both of the lift balloon systems, enabling automatic actuation of the system when towed down to the shuttle by a tow rope running through both. It allows a completely controlled and captured lift to smoothly occur, straight vertically from any offset distance. Allows use of the Dual Lift Bridge as well as the ZGM “German Method Adapter” with any contingency backup systems.
Proprietary Technology
Internal Air Systems
One of the most notable aspects of our systems is the location of the air system and all of it’s components.
-
Safely located inside the inflated envelope, the tanks, valves and associated hardware are protected from the rough handling associated with these missions. They provide less drag under tow, are less likely to get fouled on lines, kelp and obstructions and keep the system much cleaner and reduce PMS.
-
The internal air system uses proprietary quick disconnect check valves and couplers, allowing modularity of bottle configuration. In a pinch, a CRNE bottle can be used in an ExLB, and vice versa.
-
Our entire inflation system is run off of the low pressure ports on the regulator. This increases safety, decreases wear and tear and the STT IVA valve was designed to operate in this manner.
ROV/UUV Compatibility
With the shuttle and ATAC deployment method, all of our lift systems are easily integrated into ROV/UUV scenarios. with the bot needing only bring the shuttle and lines to the weight and clip on.
-
The shuttle acts as a snatch block on a tow line, being attached directly to the weight. The tow line runs through it directionally, one end to the ATAC/Balloon on the surface, the other to the tow vessel.
-
The ATAC, once towed down latches to the shuttle and fires CO2 cylinders, common to the life jackets in the system. This eliminates all firing devices, squib charges, lanyard actuation and myriad other challenges from the equation.
-
Though not certified, the shuttle is capable of being low MU by material selection alone. Attached to any length lanyard to the shape, physical offset of the entire system reduces MU signature immensely.
QR Code PMS
“Go get the manual…” Last thing anyone ever wants to hear when you are trying to get a job done. But, fact is, operators gain and lose familiarity with essentially every system over time. We are engraving QR codes on all of our key components, readable by any web enabled camera. This is a game changer for PMS and regaining proficiency after some time off.
-
Familiarity is perishible. The QR code allows the operator to quickly re-acquaint themselves with the system, the quick start guide, PMS checks and capabilities.
-
Common challenges will be addressed in a Troubleshooting tab, allowing quick resolution to a system working other than expected.
-
More than just PMS cards, the operator will have access to pre-dive, Dive Sup, Post Dive, Pre-Deployment and Turnover checklists. This should ensure that when the systems are stowed, they are stowed properly, complete and Fully Mission Capable (FMC)
Point your smartphone camera at this QR code to follow the link to the ExLB resources page.
Modularity
All of our systems are designed to use a completely modular approach to bottles employed per mission.
-
Each system is capable of deploying only the number of bottles (the heavy part) needed to conduct a particular lift.
-
With engraved depth/weight/bottle needed charts on the system, an operator can easily determine the number of bottles needed to conduct a particular lift, reducing the amount needed to charge, increasing ability to reset and repeat and potentially reducing system weight dramatically
-
This modularity extends to the air valves, connection hoses, regulators and about 30% of the chassis parts being completely system agnostic and being able to be used across the suite for contingency repair and mission completion.
Integrated 1st Stage / Bottle Valve
The use of this integrated regulator valve shed over 5# per bottle compared to the standard bottle valve, yoke and 1st stage regulator.
-
Integrated first stage and bottle valve reduces complexity, decreases variables and potential leaks and streamlines maintenance operations.
-
Dive supervisor can tell at a glance the state of charge without requiring additional tools, or even to disconnect the system.
-
Same exact valve and hose is shared by multiple platforms, reducing spare parts inventory, required training and improves casualty and critical need cross-platform modularity. In a pinch, a CRNE balloon will work with an ExLB, and vice versa.
STT Inflation Valve Assembly
The literal heart of the systems is the proprietary STT Inflation Valve Assembly. Designed and built especially to answer the specific needs of this challenge, the manual lanyard or pneumatically actuated STT IVA is far more than a simple life raft dump valve.
-
Designed with operational ease in mind, the STT IVA automatically resets itself following use, not requiring the operator to disassemble or physically replace the poppet for rearming to occur.
-
Valve is made entirely of highly corrosion resistant 316 Stainless Steel to reduce bimetallic and material corrosion. With “maintenance windows” on the back side of the poppet, the STT IVA is possibly the first valve to ever be designed to easily inspect and maintain the back side of the normally hidden assembly.
-
While most inflation valves empty the attached bottles completely, the STT IVA is designed to retain 50# of pressure in the scuba bottles, addressing the need to prevent the bottles from requiring a disassembly and visual inspection to re-pressurize, a nearly universal requirement for any completely empty bottle.